Smart Machine Box for Industrial IoT with High Performance ASIC Prototyping System
Nowadays, rotating machine is the power source for most production equipment and is widely used in manufacturing factories. Common rotating machinery mainly includes bearings, gears, shafts, and the others. However, rotating machines suffer from frequent collisions and vibrations which lead to wearing and aging, which increases the chance of failure in the overall system operation. This make the cost of factories increase and the quality of production deteriorate. Therefore, the industries gradually value the usage of accurate and efficiency predictive maintenance system.
Traditionally, predictive maintenance systems collect information of various mechanical operations with the numerous sensors equipped in the rotating machinery, and analyze the signals with specific signal processing to determine the type of mechanical fault and the remaining useful life (RUL) of rotating machines. However, the method takes a lot of time and labor cost, which is regarded as huge cost burden for most of manufacturing.
This work develops a smart machine box for industrial IoT with high performance ASIC prototyping system (HAPS), which features:
Multiple fault diagnosis technology:
During the operation of machinery, multiple fault is likely to occur because of continuous operations and contact conditions of various mechanical components. Multiple fault can be a fault combination of different mechanical components, or a multiple identical fault of a single mechanical component. Both of them make mechanical operation signals complex and unpredictable. Due to the different fault conditions, machineries show different behaviors of frequency response, which can be viewed as superposition of signals from various mechanical components. With the help of artificial intelligence, the corresponding features can be extracted from sensing signals to collect information of multiple fault.
Remaining useful life prediction:
Most sensing signals have the property of time-dependence, which can be used to predict the machinery health state with long short-term memory model (LSTM model). However, this model is hard to use for real-time calculation because of its high calculation complexity. Besides, from the view of hardware design for edge, it also brings about the high design complexity. Because the health of machine has to do with the vibrational intensity, with the help of artificial intelligence, the current root mean square values of mechanical vibrational signal is compared to the ones with fault condition to estimate the health state of machine, which can be performed the remaining useful life prediction.
Real-time operation:
The platform is developed with high performance ASIC prototyping system (HAPS) to performed the Edge AI operation. The system integrates the ADI Voyager wireless CbM sensor receiver module and wireless transceiver into HAPS. The former collects the vibrational signal from rotating machinery, and the latter upload the sensing signals to the cloud database. Consequently, the platform can process the vibrational signals and performed fault diagnosis and remaining useful life prediction in real-time.
Project Milestones
Do you want to view information on how to complete the work stage ""
or update the work stage for this project?
-
Milestone #1
Target DateIntegrate our Module - Forest into the HAPS system
-
Milestone #2
Target Date -
Milestone #3
Target Date -
Milestone #4
Target Date -
Milestone #5
Target Date -
Milestone #6
Target Date -
Milestone #7
Target Date -
Milestone #8
Target Date -
Milestone #9
Target Date -
Milestone #10
Target Date -
Milestone #11
Target Date -
Milestone #12
Target Date -
Milestone #13
Target Date
Team
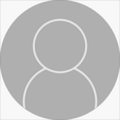
Comments
Adding new milestones
Architectural Design stage currently has three sub-stages:
Specifying a SoC
Work through the items needed to specify the highest level of design for the SoC.
IP Selection
Pick the IP parts from the Technology section. You might also want to think about your Project Structure and other high level Design Flow considerations.
Verification
You should start to think about how you will validate your SoC design. Creating verification and validation assests as you develop the design is a good working practice.
You should find some helpful examples from some of the other SoC Labs projects.
Happy to help and answer any questions.
Updates to milestones (end of June 2024)
Hi,
As we are now into the start of July it would be good to get an update on your milestones at the end of June. If you need any help or support for the project please let us know. We look forward to hearing from you.
John.
Picture of your Architecture
Hi,
I think it would be helpful if you could add a diagram of the system architecture to the project. That will make it easier for people to understand the system and the the work that is needed. Can you add one?
Picture of your Architecture
Have you made any changes to the last system architecture you proposed?
Updated milestones
Hi,
As we are now into the start of October it would be good to get an update on your milestones at the end of September.
We need to understand if it is likely you will be making progress so we can progress a tape out.
If you need any help or support for the project please let us know.
We look forward to hearing from you.
Update on your project
It was good to see the project demonstrated at APCCAS. It would be nice to see a update on the project here if possible. The last update was: Milestone #1
Target Date
August 1, 2024
Integrate our Module - Forest into the HAPS system
It would be very helpful to explain what processing of the incoming 'Sending Data' is done on the Arm CPU in the PS and how the feature extraction is done?
Can you add some more detail
Could you add some details on the IP blocks and AXI connections you have added to the programmable logic (PL). We don't need to know the detail of the Forest implementation of your custom IP. What would be helpful is to know how the parts of the system communicate and data flows around the system.
The rest of the team
It would be nice if the other members of the team could add themselves to the project< Hus-Chi Chen, Pin-Ching Shen, Yen-Chen Yen.
Add new comment
To post a comment on this article, please log in to your account. New users can create an account.